A Project-Oriented Decision Support System for Production Planning in Make-to-Order Manufacturing
by Tamás Kis, Gábor Erdös, András Márkus, József Váncza
It has become quite common for make-to-order manufacturing industries to use the project-oriented approach for planning production runs on various time scales. In this approach a project consists of tasks, each of which represents a manufacturing process. The connections between the tasks are captured by precedence constraints. Due to the physical characteristics of these processes, the 'intensity' of performing the tasks varies over time. At SZTAKI, new planning software has been developed which is able to adequately model the varying intensity of tasks and the flow of information and material between them.
In project-oriented production management each customer order becomes a project that must be carried out from the ordering of material, through product design, to production and delivery to the customer. Standard planning software packages model the tasks by rectangles, assuming uninterrupted execution and a constant rate of resource usage. Moreover, the precedence constraints between the tasks express only temporal relationships, while the information and material flow between pairs of overlapping tasks are neglected. This makes it very difficult to realise the generated production plan.
In order to create realistic production plans, a new decision support system has been developed in one of the thematic clusters of the three-year 'Digital Factories' R&D project supported by the National Research and Development Project in Hungary. The project started in July 2001 and finished in March 2004. The work was carried out by the Engineering and Management Intelligence Laboratory of SZTAKI in collaboration with the Miskolc University of Technology and the Machinery Plant of General Electric Consumer & Industrial in Hungary.
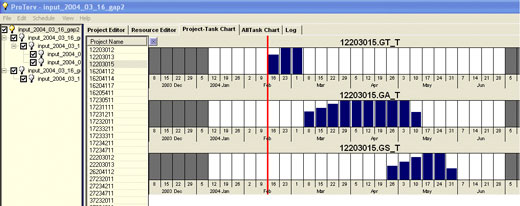 |
Figure 1: Screen of the planning software. |
Our software supports planning with variable-intensity tasks, where the flow of information and material is captured by 'feeding-precedence' constraints between the tasks (defined below). Its graphical user interface helps human planners develop a number of plan variants, organised in a tree hierarchy. The variants may differ in the time windows of the projects, the set of projects selected for planning and the resource capacity (Figure 1). The software obtains all project and resource data from the information system of the plant through file exchange. It was an important requirement to keep the response time short, thereby allowing the users to work interactively with the system.
Modelling with variable-intensity tasks and feeding-precedence constraints
A variable-intensity task is one in which the amount of work spent on the task may vary during the execution. In actual production, tasks usually start at a low intensity during preparations which then gradually increases to a maximum. The resources needed to complete a task are consumed proportionally to the varying intensity. The output of the task may be used in downstream production prior to the completion of the whole task. To model this situation, we introduced the notion of a feeding-precedence constraint between a pair of tasks A and B, with parameter p specifying that p percent of task A must be completed before task B may be started and that task B cannot advance faster than task A (see Figure 2).
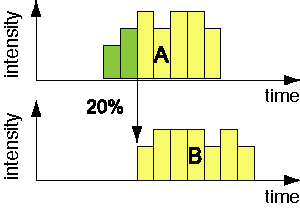 |
Figure 2: Feeding precedence constraint from task A to task B with p = 20%. |
Techniques employed
The planning problem has been modelled and solved by mathematical programming techniques using cutting planes. The planning module (PM) is based on a commercial integer-programming solver. The PM can optimise various objective functions that occur in practice, such as minimising the extra capacity needed to complete all projects, or the weighted tardiness. The short response time of the system on real-life problems makes it suitable for interactive decision support.
The PM has been embedded into a software package which assists the work of planners by offering features such as displaying the structure (tasks and precedence) and the status (work done on each task) of the projects. The package also provides editing functions, including modification of project time windows or resource capacities, and supports the systematic elaboration of plan variants organised in a tree hierarchy. This allows decision makers to choose the final plan from a set of alternatives.
Application areas
The system is suitable for solving production-planning problems in make-to-order manufacturing where the tasks of a project represent aggregated activities. Another domain of application exists when only the production must be scheduled, but on different time horizons. A long-term plan (thirty weeks) can be generated by the planning module, and based on this, the weekly schedules can be obtained by an appropriate short-term scheduler. We have developed a pilot system for each of these application domains.
There are a number of key benefits of our project-oriented production-planning system. Planning with variable intensity tasks and feeding precedence constraints results in more accurate production plans. This, along with the combination of project execution and resource capacity planning leads to a better due-date observance and to a better use of resources. As a result, more customer orders can be accepted and production costs are reduced.
The techniques employed in the planning module can be applied in various settings. Current work is focusing on improving the robustness of the planning module and making the user interface capable of communicating with standard, widely used ERP systems.
Please contact:
Gábor Erdös, Tamás Kis, András Márkus, József Váncza, SZTAKI, Hungary
Tel: +36 1 279 6156, +36 1 279 6299
E-mail: gabor.erdos sztaki.hu, tamas.kis sztaki.hu, markus sztaki.hu, vancza sztaki.hu
|