COSMOS: Safe and Optimal Operation in Complex Industrial Systems
by Péter Inzelt
COSMOS, a three-year project within the framework of the National Research and Development Programs, commenced in the middle of 2001 with the aim of developing a novel, knowledge-intensive technology for safe and optimal operation in large and complex industrial systems. The project, led by SZTAKI, is carried out by a consortium consisting of both academia and industry.
Safety and optimality of operation are decisive factors for large and complex industrial systems due to their complexity and the uncertainty associated with their functioning. The project COSMOS aims to develop a novel information technology applicable in complex industrial systems for process parameter monitoring, early detection and diagnosis of equipment and technology faults, and fast detection of malfunction roots.
The project partners include SZTAKI, the Atomic Energy Research Institute at the Hungarian Academy of Sciences (MTA KFKI), the Department of Control Engineering and Information Technology and the Department of Measurement and Information Systems at the Budapest University of Technology and Economics, Paks Nuclear Power Plant Ltd, and MOL Hungarian Oil and Gas Plc.
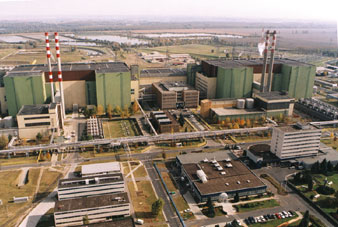 |
The Nuclear Power Plant in Paks, one of the two application sites (courtesy by NPP). |
The System
The technology to be developed will offer operational support for process devices through advice given to the operator. It will present user-friendly and efficient interactive tools for storing technology-related knowledge, on-line modeling of process phenomena, visualisation of diagnostics information, and the on-line display of advisory documentation to be used during fault-corrective actions.
The kernel of the software system is represented by a central database, with a static part consisting of the following three main elements:
- the 'Object Structure Definition (OSD)', which describes the features and attributes of the different objects handled by the system
- the 'Abstract Object and Knowledge Repository (AOR)', which acts as the repository for the objects described in the OSD
- the external databases, handled in their original form, but using standard interfaces.
The running programs perform their operations over an instant (fast) database (IDB), which constitutes the dynamic part of the central database. An IDB can be formed only from the objects stored in the abstract repository and it always contains as many objects as are required by the processing modules running at the time.
The modules are used for establishing a structured storage for the engineering-technical information concerning the components of the complex industrial system, and for the preliminary analysis of the safety, operational and ergonomic consequences of the planned reconstructions and changes in the applied technology.
The 'Configuration and Document Handling Module' is used for storing basic, technically relevant information concerning the different objects (buildings, technological systems, equipment etc). For documents directly connected to the operation of the plant, the system ensures access to the on-line database of the process information system, in order to retrieve and display the process parameters (measured or calculated signals) which are referenced in the document.
The 'Virtual Reality Module' is connected to VRML models converted from the 3D CAD drawings of the rooms and the equipment, and is used for performing the following basic tasks:
- the VR Training Component models potentially dangerous activities, trains work operations, and plans the optimal work
- the VR Design and Validation Component is used for planning and modeling plant modifications and reconstructions in an optimal way, and for checking their conformance to the standards and requirements
- the VR Decommissioning Component is used for planning and modeling the dismantling of hazardous facilities and equipment.
Monitoring the technological process, the 'Early Fault-Detection Module' identifies deviations from the normal state using the principle of analytic redundancy, ie, process measurements and on-line calculations based on the components model.
The 'Fault Diagnostic Module' identifies the root causes of equipment faults or system malfunctions. Having the fault trees, which are defined by an interactive fault-tree editor, the reliability of the minimal cuts can be determined. This information can be used for identifying the most 'fault-sensitive' components, and for determining the relative probabilities of root causes creating specific fault symptoms. For large subsystems, the root causes are determined by an on-line fault-tree evaluation procedure.
The actual operational conditions for technological subsystems and equipment efficiencies are determined by the on-line 'Process Optimisation Module', based on on-line process measurements and background calculations. Using this module, the experts can assess the position of the actual working points with respect to the optimal states.
In its final form, the developed technology will constitute a general-purpose, open-architecture software shell providing the operators of various industrial systems with efficient support. It will realise the following principle: an industrial system should be able to operate safely while simultaneously working close to its optimum capacity.
Results and Applications
The results will be implemented at the Nuclear Power Plant in Paks, firstly for experimental use at the central supervisory computer, and later at the supervisory systems of the nuclear block. Another implementation will be used by MOL Ltd, in the supervisory system of the network of high-pressure natural-gas pipelines in Hungary. According to the schedule of the project, the development of the prototype database, prototype interfaces, prototype functional modules and final interfaces has been successfully finished.
Link:
http://www.sztaki.hu/sztaki/projects/html/cosmos.jhtml
Please contact:
Péter Inzelt, SZTAKI
Tel: +36 1 279 6184
E-mail: inzelt@sztaki.hu
|